Manufacturing Processes for Polypropylene Bushings
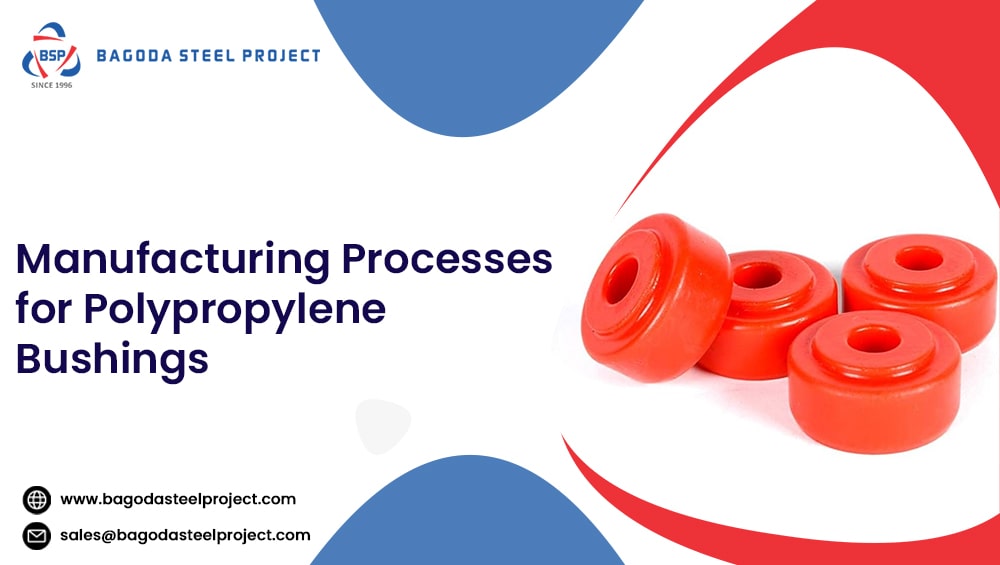
Manufacturing Processes for Polypropylene Bushings
Polypropylene bushings, frequently heroes behind the scenes in infinite packages, play a vital function in lowering friction, protective components, and making sure smooth operation in equipment. But how do these flexible components come to life? Let's delve into the charming global of polypropylene bushing production, exploring the key approaches that transform plastic granules into reliable mechanical workhorses.
Understanding Polypropylene:
Polypropylene (PP) is a flexible thermoplastic polymer regarded for its marvelous electricity, lightweight nature, and notable chemical resistance. These properties make it a famous desire for production of various components, which includes bushings. Polypropylene bushings provide advantages like:
Reduced Friction: They help limit put on and tear on mating surfaces.
Corrosion Resistance: They face up to exposure to many chemicals and environmental elements.
Cost-Effectiveness: Compared to metallic bushings, they're frequently cheaper.
Lightweight: They make a contribution to reduced overall weight in machinery.
Dimensional Stability: They keep their shape under varying loads and temperatures.
The Journey of Polypropylene Bushings:
The production system for polypropylene bushings can vary relying at the favored bushing size, complexity, and precise utility necessities. Here's a breakdown of the most common methods:
Raw Material Preparation: The journey begins with superb polypropylene granules, carefully inspected and dried to cast off any moisture that would affect the very last product's residences.
Selection of the Manufacturing Process:
Injection Molding: This is a widely used method for producing excessive-quantity, complicated polypropylene bushings. The procedure involves melting the dried granules and injecting them right into a pre-designed mold hollow space beneath excessive pressure. Once cooled, the completed bushing is ejected from the mildew.
Extrusion: Suitable for developing long, continuous lengths of bushings, extrusion entails melting the polypropylene granules and forcing them via a die with the preferred bushing profile. The extruded cloth is then cooled and reduced to the specified lengths.
Machining: This approach makes use of a lathe or CNC machine to precisely form pre-fashioned polypropylene inventory into the favored bushing dimensions. This method is regularly used for creating custom or low-quantity bushings.
Mold Design and Tooling: (Applicable to Injection Molding) For injection molding, developing a unique mildew hollow space with the preferred bushing design is crucial. Factors like bushing size, tolerance necessities, and gating systems are all taken into consideration all through mildew design and tooling.
Material Blending (Optional): In a few cases, producers may additionally blend polypropylene with components like lubricants, antioxidants, or flame retardants to beautify unique properties of the bushings for his or her intended packages.
Quality Control: Throughout the manufacturing process, rigorous best-managed measures are implemented to make sure bushings meet the specified specifications. This may involve dimensional checks, floor finish inspection, and material belongings checking out.
Finishing and Secondary Processes (Optional): Depending on the utility, extra procedures like deburring (casting off sharp edges), surface treatments, or printing of trademarks or markings might be done at the finished bushings.
Factors Influencing Manufacturing Choices:
Several elements influence the choice of the producing system for polypropylene bushings:
Bushing Size and Complexity: Injection molding is suitable for complex shapes and high volumes, even as extrusion is ideal for long, simpler profiles. Machining gives flexibility for custom designs but can be restricted in manufacturing pace.
Production Volume: Injection molding is greener for high-volume production, while machining is better suitable for small quantities or prototypes.
Cost Considerations: Factors like tooling fees, material usage, and manufacturing velocity influence the general cost-effectiveness of every method.
The Future of Polypropylene Bushing Manufacturing:
The global of polypropylene bushing manufacturing is continuously evolving, with improvements like:
3-D Printing: Additive production technologies using polypropylene filaments have the potential to create complicated bushings with difficult designs.
Sustainable Practices: Utilizing recycled polypropylene content in bushing production is gaining traction, minimizing environmental effect.
Advanced Material Science: Research on developing specialized polypropylene blends with more advantageous homes for unique applications is ongoing.
Conclusion:
Polypropylene bushings are a testament to innovative production strategies. Understanding the various strategies involved in their creation offers treasured perception into the world of polymer engineering and the flexibility of this essential material. By selecting the right technique and cloth mixture, producers can create excessive-overall performance polypropylene bushings that contribute to the easy operation of machinery throughout diverse industries. Need excellent polypropylene on your subsequent bushing assignment? Look no further than Bagoda Steel Project! We provide an extensive variety of polypropylene grades and assist you to select the right cloth in your specific desires. We also partner with dependent suppliers who utilize superior manufacturing processes to ensure the manufacturing of pinnacle-notch polypropylene bushings.
